Mechanical Properties
The mechanical properties among all the properties of plastic materials are commonly the most important ones since virtually all the service conditions and the majority of the final applications involve some degree of mechanical load.
The selection of the aproppriate degree for a certain application is based frequently on the selection of mechanical properties such as Impact Resilience, Rigidity and Tensile Strength. The chart values of plastics mechanical properties are determined from tests made in a laboratory under standard conditions. As regards the practical application, the materials do not depend on a simple and continuous deformation, besides being subject to adverse environmental factors. That is exactly what is mentioned in the part describing the relation of mechanical properties with temperature and strain rate.
The basic understanding of stress-strain behavior of plastic materials is highly important to comprehend the physical meaning of mechanical properties. The stress-strain diagram charted in the figure is described as follows. Defining some terms related to it is necessary for a better understanding of this diagram.
Stress: strength applied in order to produce strain in a unit area of a test specimen. It is the relation of load applied to the original cross sectional area.
Strain: relation of elongation to original length (Δl/l). It is expressed as a dimensionless relation.
Elongation: increase of the test specimen length generated by load stress.
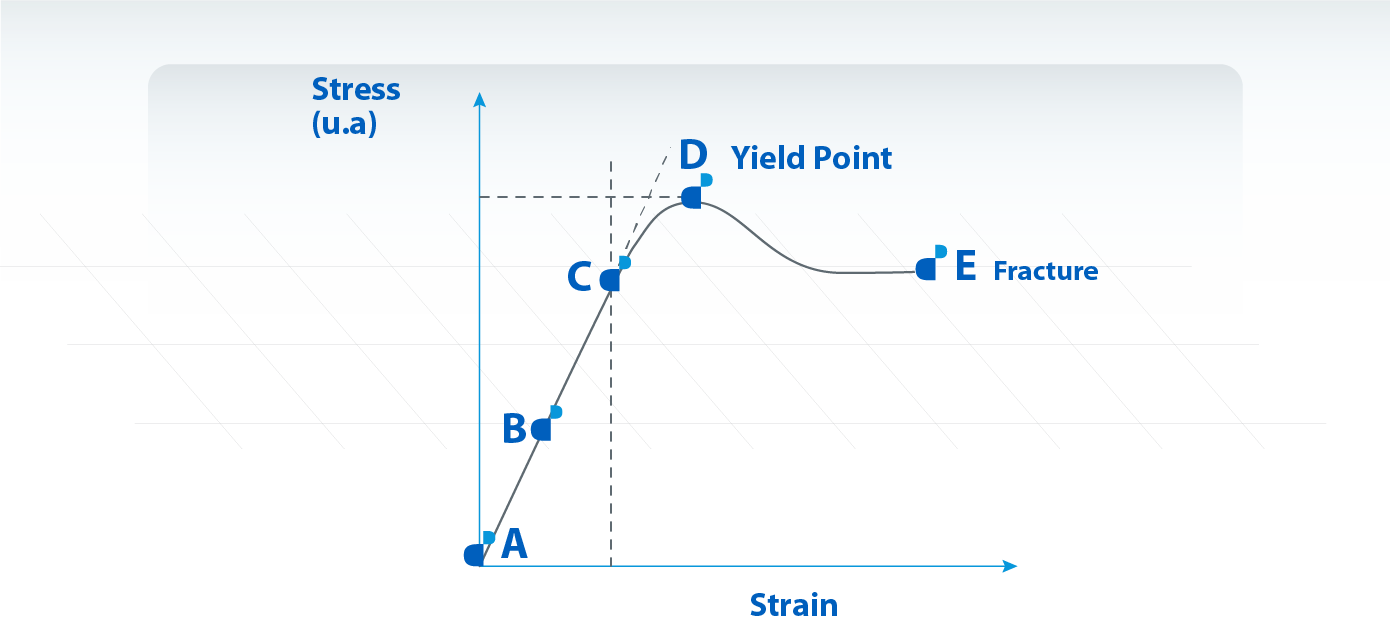
Having defined those parameters, we will analize in deep the diagram in order to examine what type of information could be obtained from it and how that information is related to the material’s properties.
Stress in the proportional limit: the greatest stress under which the material is able to mantain the load without any deviation stress-strain proportionality (Hooke Law). Plastic behavior under the proportional limit is elastic and, thus, the deformations are recoverable deformations. This part of the curve represents the total utility range for most applications. It is not common for manufactured products to be useful for their appliance if the stress to which they will be subject exceed that point. This stress value is properly marked in the stress-elongation diagram of figure C.
Tensile stress at yield: the first point at which there is an increase in the strain without a stress increase. Unless stated otherwise, this stress is the one corresponding to the yield point. In the stress-strain diagram, the yield point is marked with D.
Maximum resilience: the greatest unit stress that a material resists when being subject to a load applied by compression, tension or cut. Any increase in the tension whatsoever leads to fracture of the specimen. In the diagram stress-strain the yield point is marked with E.
Elongation at Yield: variation of the specimen length from the beginning of the elongation to the yield point.
1 Elasticity modulus at Bending
It is a measure of the capability of a material to support the sag when being subject to a load applied perpendicularly to the longitudinal axis. The bending module is represented by the initial slope of the curve stress-strain. A high value of this slope (high module) implies that the component has a high degree of rigidity.
2 Elasticity Modulus at Shear
Shear modulus is one measure of the rigidity and resilience the material offers during the torsion process. It is precisely measured in a torsional pendulum by placing a rectangular specimen and giving it an inertia moment known by calculating the amortization of the free oscillation.
Like the elasticity modulus in bending, it is a measure of the rigidity of the component and it is estimated in force per unit area.
3 Elasticity modulus at Yield
It is a measure of the resilience the material offeres during the elongation process. It is a highly important test since the material in the different applications are frequently subject to these types of forces.
4 Resilience to Impact
It is a tenacity measure of the material, i. e. the resin’s capability of absorbing a certain stress without fracturing. The energy required for breaking the specimen is the combination of energies necessary to deform, initiate and expand the fracture and to finally push the remaining ends.
In the diagram stress-strain, the tenacity derives from the area under the curve. A material with higher resilience to impact will show a greater area under the curve. It is worth mentioning that the rate of strain will be considerably higher in tests of resilience to impact than in rigidity tests.
In practice, the resilience to impact is generally determined by two different methods: IZOD and Charpy. In both cases, the objective of the test is to measure the resilience degree of a specimen to the impact of a pendulum loaded with a certain weight. The result is expressed in terms of the kinetic energy consumed by the pendulum so as to fracture the specimen. The specimen may or may not have a neck but the values obtained with neck specimens are generally more precise since the fracture being generated is brittle and non-ductile.
The difference between IZOD and Charpy methods lies in how the specimen is placed inside the machine. While in IZOD method the specimen is placed vertically and the pendulum strikes at one end, in Charpy method the specimen is placed horizontally and the pendulum strikes at the central part of it. (See image)
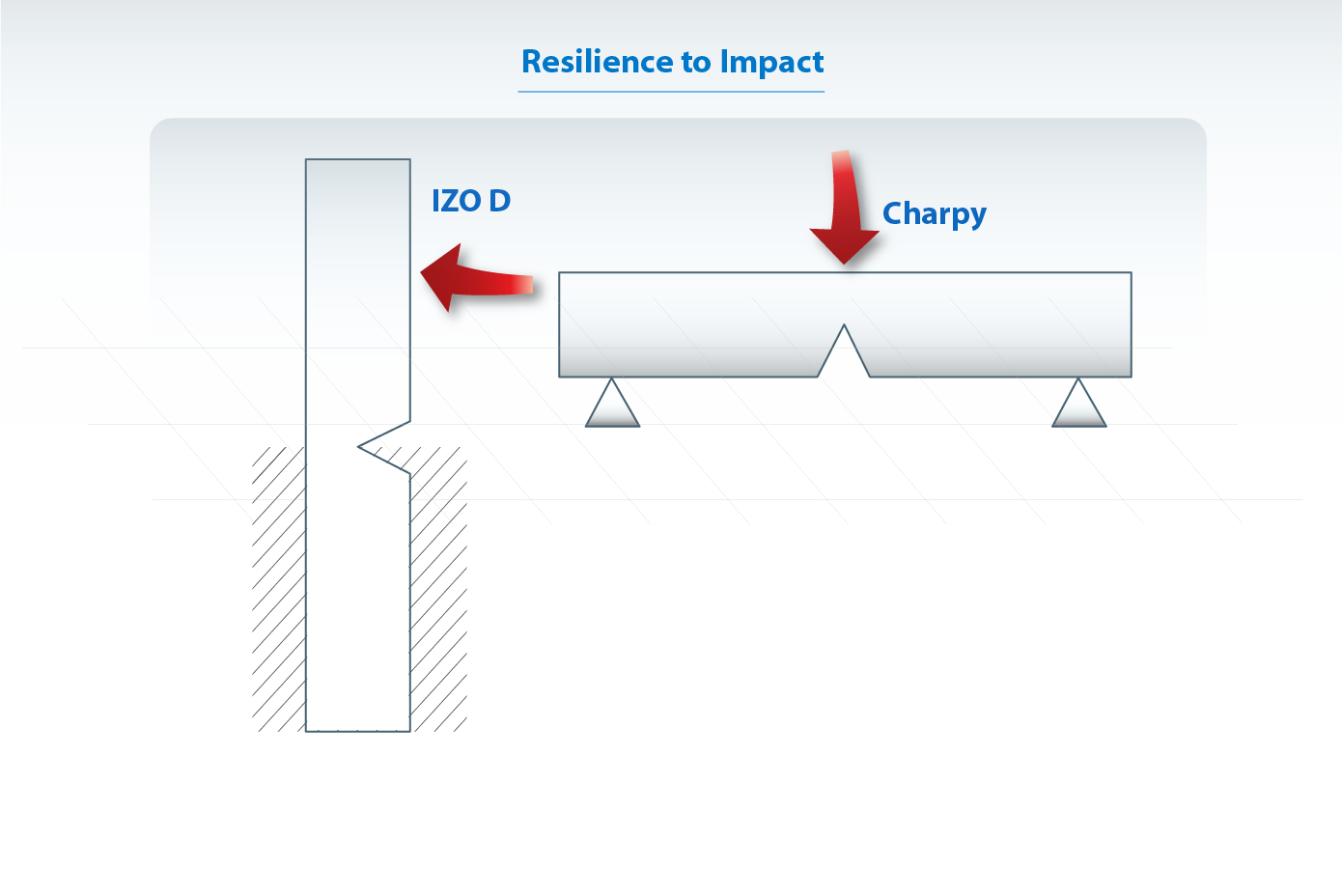
5 Relation Mechanical Properties – Temperature – Rate of Strain at Shear
We have been analyzing the features of the stress-elongation curve in general terms so far. It is worth mentioning that the shape of that curve depends notably on both the rate with which the force is applied and the temperature at which the test is being perfomed. Below the typical temperature known as glass transition temperature, the material has high rigidity but low resilience to impact. Materials under such temperature conditions have limited movements and the only way for dissipating energy is to create new areas fractured at applied slight strains.
That is the case of the curve A in the diagram. This same material tested at a higher temperature will show a behavior of the curve B type with higher tenacity (greater area under the curve) and less rigidity than the other curve.
Likewise, if tested at a constant temperature but at a very high strain rate, the material’s behavior would have been similar to curve A. However, if tested at a low strain rate, the behavior would have been similar to curve B. This dependency of properties on the conditions establishing them should be considered when analyzing the possibility of using a certain material for a certain application.
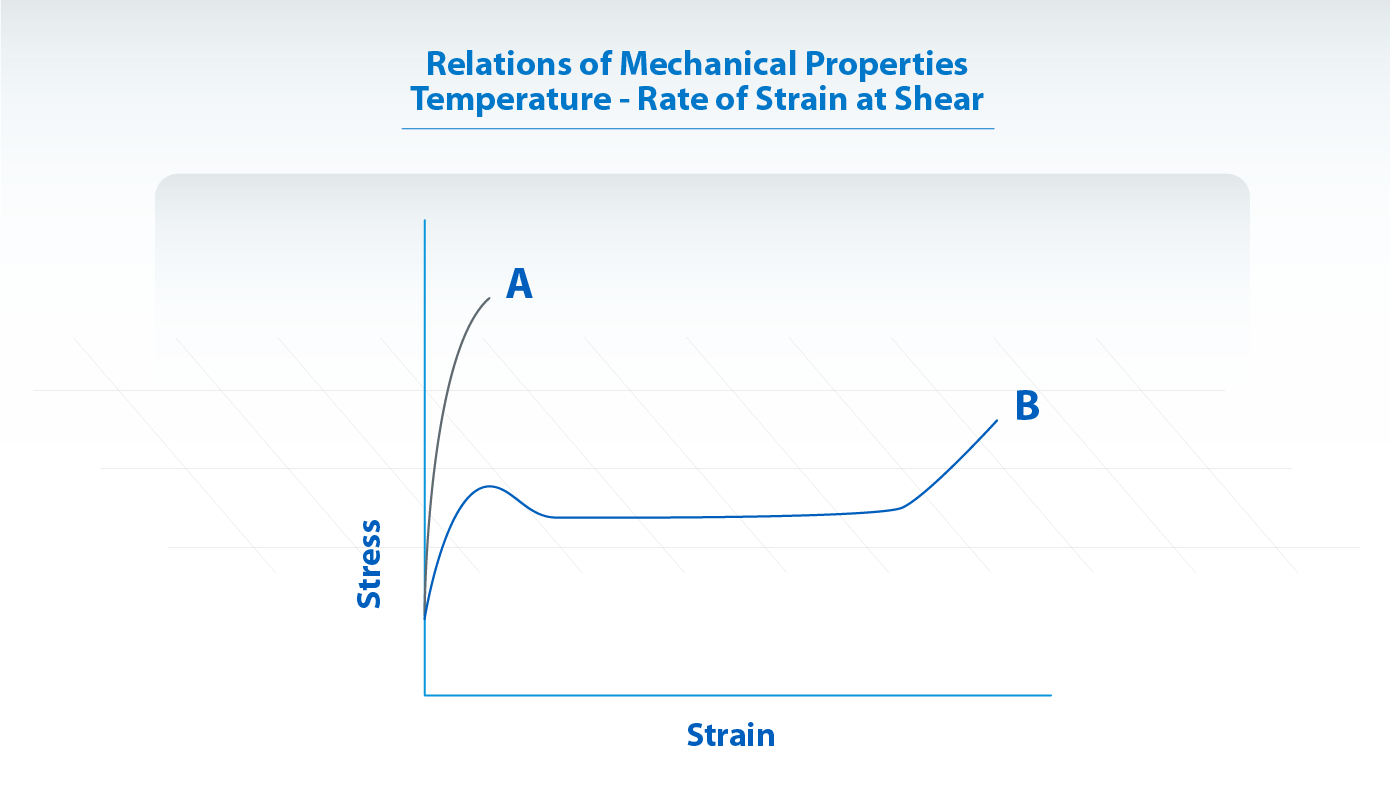
6 Properties of Cuyolen and Cuyotec Polypropylenes
Sometimes, materials with high rigidity show poor impact properties while materials with tenacity have lower bending modulus.
Cuyolen and Cuyotec materials show a good balance between that two characteristics, which makes them appropriate for many applications. In the figure, it is represented the relation rigidity-tenacity of Cuyolen and Cuyotec homopolymers and copolymers.
